O setor industrial está em constante crescimento e é um dos mais exigentes do país. Nesse contexto, investir em máquinas industriais se torna essencial para impulsionar a economia e otimizar a produção. Com a evolução dos processos e o surgimento de novos empreendimentos, adquirir equipamentos modernos permite acompanhar o desenvolvimento e atender às demandas do mercado.
No entanto, à medida que novas tecnologias são incorporadas, surgem também diversos desafios. Você já se perguntou por que uma máquina ou componente falha ou fratura durante o serviço? E mais importante: como isso poderia ser evitado? Essas questões estão diretamente ligadas à análise de falhas na indústria de máquinas.
Diante desse cenário, a Engenharia de Materiais exerce um papel fundamental. Um dos principais recursos para prevenir falhas e avaliar não conformidades no processo produtivo é a análise de falhas em materiais industriais.
O que é a análise de falhas?
A análise de falhas é um processo investigativo que, por meio de técnicas laboratoriais, busca identificar as causas de um comportamento indesejado em um material, como fraturas, trincas ou desgastes excessivos.
Primeiramente, deve ser feita a identificação do local e da gravidade da falha. Em seguida, realiza-se uma análise macroscópica e formulam-se hipóteses sobre as possíveis causas. Depois disso, são conduzidos ensaios mecânicos para testar as amostras, como:
- Ensaio de tração
- Ensaio de compressão
- Ensaio de flexão
- Ensaio de fadiga
Com os resultados obtidos, discute-se as hipóteses e avalia-se a existência de mecanismos que possam prevenir novas ocorrências. Por fim, analisa-se a recorrência e a severidade da falha para definir ações corretivas.
Você pode conferir mais sobre esse processo aqui: https://www.labteste.com.br/ensaios-mecanicos-e-analises-falhas?
Qual a importância da análise de falhas para as empresas?
Para garantir alto desempenho na indústria de máquinas e evitar prejuízos financeiros, é fundamental manter os equipamentos em boas condições de funcionamento. A análise de falhas em materiais desempenha um papel essencial nesse aspecto, prevenindo quebras, trincas e mal funcionamento de componentes.
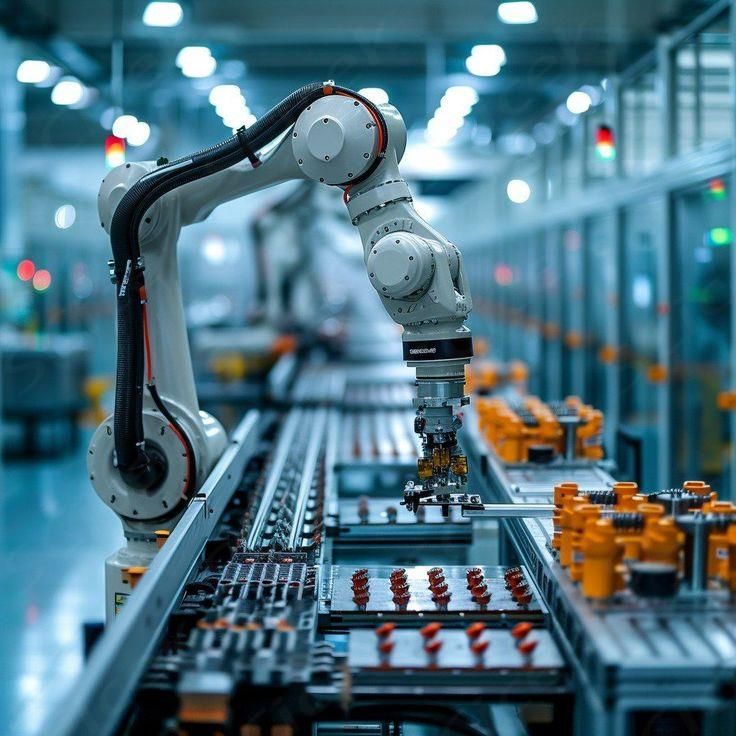
Além disso, esse processo também contribui para:
- Aprimorar técnicas de produção;
- Garantir um fluxo constante de operações;
- Aumentar a segurança dos trabalhadores;
- Otimizar a lucratividade.
Portanto, é fundamental que sejam estabelecidos parâmetros em conjunto com os setores de manutenção e gestão.
Caso real: falha em componentes na indústria automotiva
Um exemplo real da importância da análise de falhas ocorreu na indústria automotiva. Um fabricante de autopeças enfrentou um alto índice de reclamações sobre a ruptura prematura de eixos de transmissão. O problema gerava custos elevados com recalls e comprometia a segurança dos veículos.
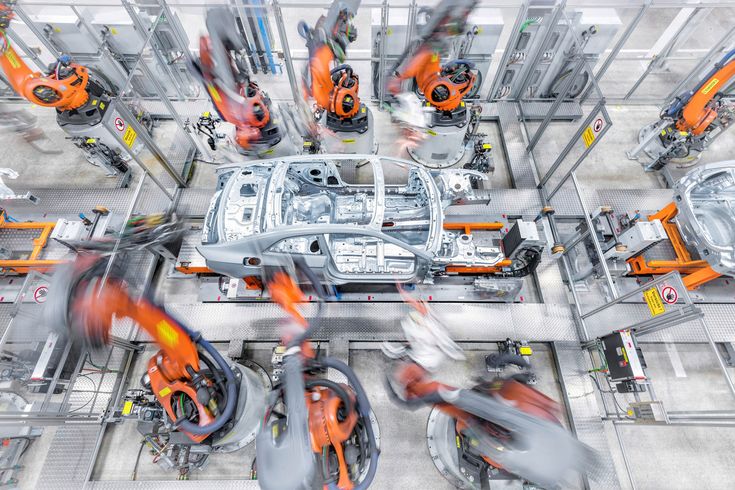
Inicialmente, suspeitou-se de erro de montagem ou lubrificação inadequada. Entretanto, a investigação revelou que o material do componente não possuía a resistência necessária à fadiga exigida pelo projeto. Através de ensaios laboratoriais, como análise de dureza, microestrutura e ensaios de fadiga, verificou-se que a têmpera aplicada era insuficiente em alguns lotes, comprometendo a vida útil do eixo.
Com base nesses dados, ajustes foram realizados no controle de temperatura do forjamento e nos tratamentos térmicos, eliminando o problema e aumentando significativamente a vida útil dos componentes. Esse caso ilustra como uma análise adequada dos materiais pode evitar falhas, melhorar a qualidade do produto e reduzir custos operacionais.
Para saber mais sobre análise de falhas conforme as normas técnicas, veja a ABNT NBR 6158 – Diretrizes para Análise de Falhas.
Como a EJEM pode ajudar?
A EJEM está diretamente envolvida na solução de problemas enfrentados pela indústria de máquinas. Nossa atuação abrange a verificação de propriedades e características de materiais que apresentam falhas no sistema produtivo.
Na prática, a análise de falhas está presente no escopo de diversos projetos da EJEM, utilizando técnicas que vão desde ensaios mecânicos, como tração, compressão, flexão, impacto e fadiga, até a caracterização microestrutural, que permite detectar trincas, falhas e inclusões de maneira detalhada.
Assim sendo, nosso objetivo é identificar falhas, investigar suas causas e otimizar processos para que sua empresa possa evitá-las, garantindo maior segurança, eficiência e redução de custos.